Introduction
The Challenge
Separation processes involving gas/liquid or liquid/liquid phases are widely utilized in various industries, yet they present significant challenges. The packing material in packed columns must enhance the surface area for effective mass transfer while minimizing the pressure drop as much as possible.
Structured packing has been in use for 40 years and has not evolved much during that time. The folded steel configuration creates numerous channels that connect to the vessel wall, leading to a high demand for re-distribution and issues such as increased pressure drop, channeling, foaming, and flooding.
Inspired by Nature
Advancements in production and design techniques now enable the creation of more efficient shapes.
SpiroPak features a complete 3D design that promotes a smoother flow within the packed bed. Its spiral configuration provides excellent contact surface area while reducing unnecessary turbulence and pressure drop.
Pressure Drop
Being one of the most important process parameters, the pressure drop of SpiroPak has been thoroughly assessed in various setups. An example result can be seen below. In this case pressure drop of SpiroPak has been compared to standard packings used in industry. The set-up is a 200mm column, and 400mm packing height. Air is introduced at different flow rates and liquid rate (water) is kept constant.
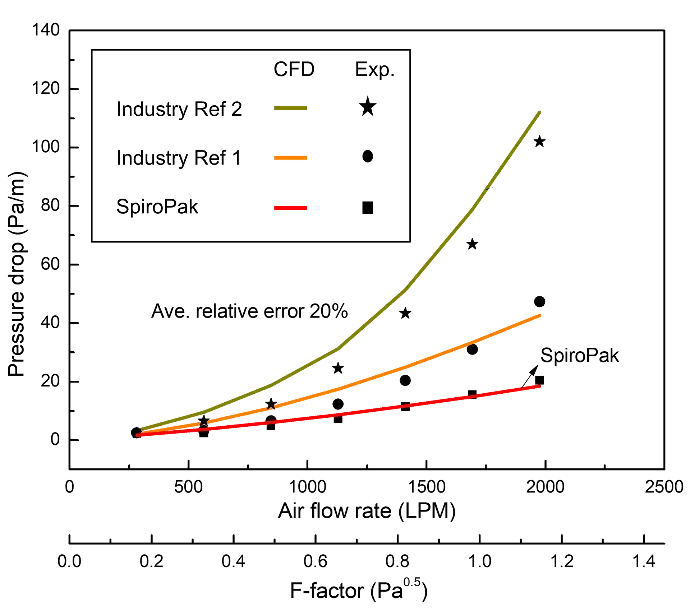
Significantly lower pressure drop
This graph clearly shows the lower pressure drop achieved by SpiroPak. It should be noted that differences become even more pronounced at higher F-factors. Most industrial applications will run at F-factors up to 3.
CFD (Computational Fluid Dynamics)
Another interesting point to note is the alignment of the results and the CFD model that has been prepared. This provides us with the tools to predict behaviour very accurately.
Mass Transfer
Mass transfer is the movement of molecules from one phase or location to another, driven by a concentration gradient. It plays a critical role in many industrial processes, such as distillation, absorption, extraction, and chemical reactions.
In mass transfer operations, two or more phases—such as liquid and gas—are brought into contact, allowing specific components to move between them. For example, in a distillation column, lighter components transfer from the liquid phase to the vapor phase, enabling separation.
Efficient mass transfer depends on maximizing the contact area between phases and ensuring optimal flow dynamics. Structured packing and similar technologies are designed to enhance these conditions, improving the efficiency and performance of mass transfer processes in applications ranging from chemical manufacturing to environmental systems like carbon capture.
CO2 Mass transfer test
In our test setup we evaluated the mass transfer efficiency of SpiroPak compared to an industry reference (Mellapak 250Y). In the following graph it can be seen that the mass transfer for SpiroPak is higher than industry reference.
Note
The test is conducted at relatively low F-Factor. It can be seen that the benefit of SpiroPak increases at higher F-Factors and this continues to values well beyond the floading value for the industry reference.
Furthermore, the higher mass transfer in this case, is achieved at lower pressure drop.
Foaming
Foaming is a critical issue in processes utilizing structured packing because it disrupts the delicate balance of mass transfer between the liquid and gas phases. Structured packing is designed to maximize surface area, enabling efficient interaction between fluids. However, foaming introduces several complications:
- Reduced Efficiency: Foam acts as a barrier, obstructing the intended pathways for gas and liquid flows. This hinders the contact between phases, significantly decreasing mass transfer efficiency.
- Pressure Drop: Foam accumulation increases resistance to gas flow, causing a higher pressure drop across the packed column. This can impact process control and energy efficiency.
- Flooding Risk: Excessive foaming can lead to liquid holdup and flooding, where the liquid overwhelms the packing structure. This results in poor separation performance and potential operational shutdowns.
- Difficulty in Control: Foaming behavior is often unpredictable and varies with process conditions, making it challenging to maintain consistent operation.
When evaluated alongside the industry reference product, it is apparent that the reference product has a pronounced tendency to foam, whereas SpiroPak exhibits no foaming under the same processing conditions.
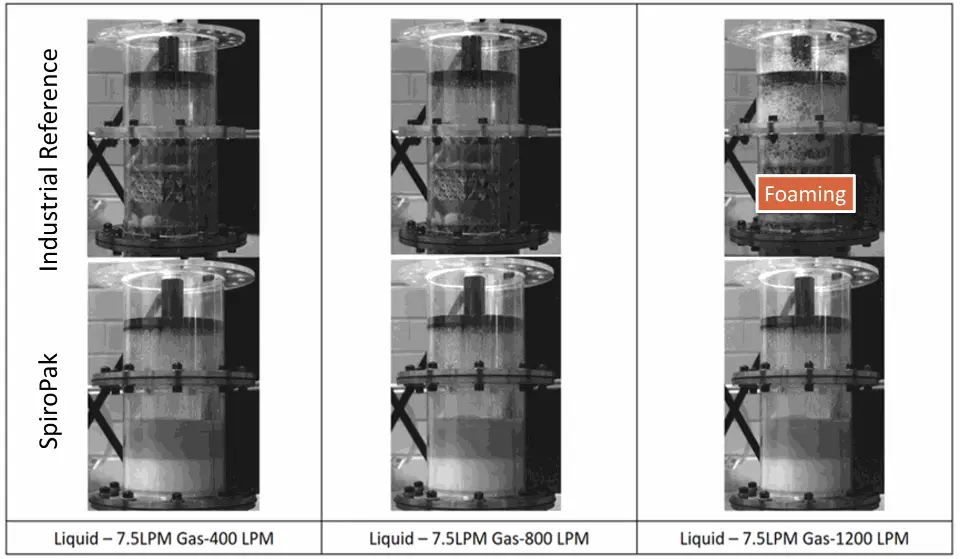
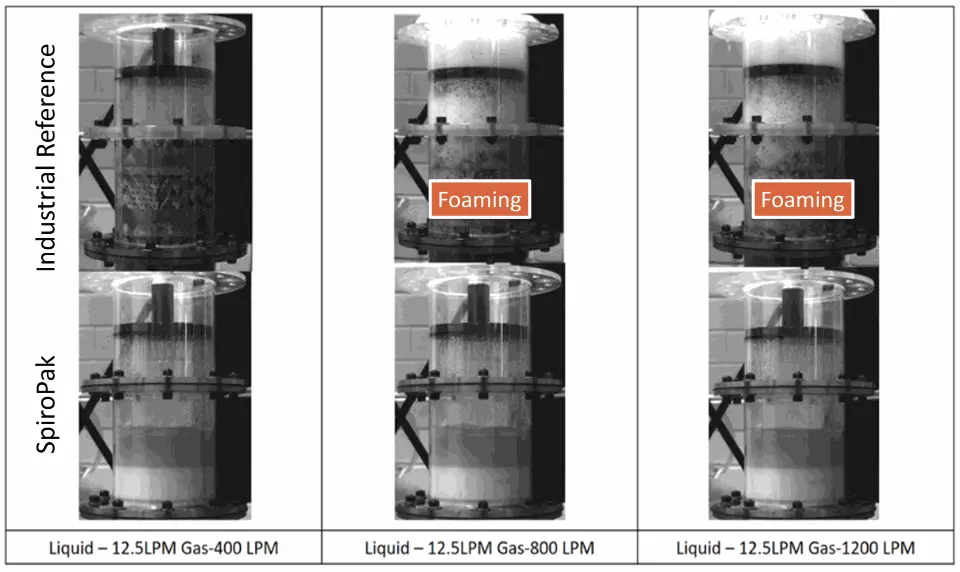
The system used is air and water with a small amount of detergent.
Fouling
Fouling, the accumulation of unwanted materials on surfaces within the packing structure, introduces several problems:
- Reduced Surface Area: Deposits cover the intricate surfaces of the structured packing, reducing the area available for effective mass transfer and impairing separation performance.
- Flow Obstruction: Fouling narrows the channels within the packing, disrupting the intended pathways for liquid and gas flows. This leads to uneven distribution and reduced efficiency.
- Increased Pressure Drop: Accumulated fouling material creates resistance to gas flow, causing a significant increase in pressure drop, which can impact process economics and energy usage.
- Liquid Maldistribution: Fouling disrupts the uniform spread of liquid over the packing surface, creating dry or stagnant zones that further impair the mass transfer process.
- Frequent Maintenance: The presence of fouling necessitates more frequent cleaning or replacement of packing, leading to increased operational downtime and maintenance costs.
- Corrosion and Degradation: In some cases, fouling materials may promote corrosion or degrade the packing material itself, shortening the equipment's lifespan.
SpiroPak has been evaluated against an industry reference packing.
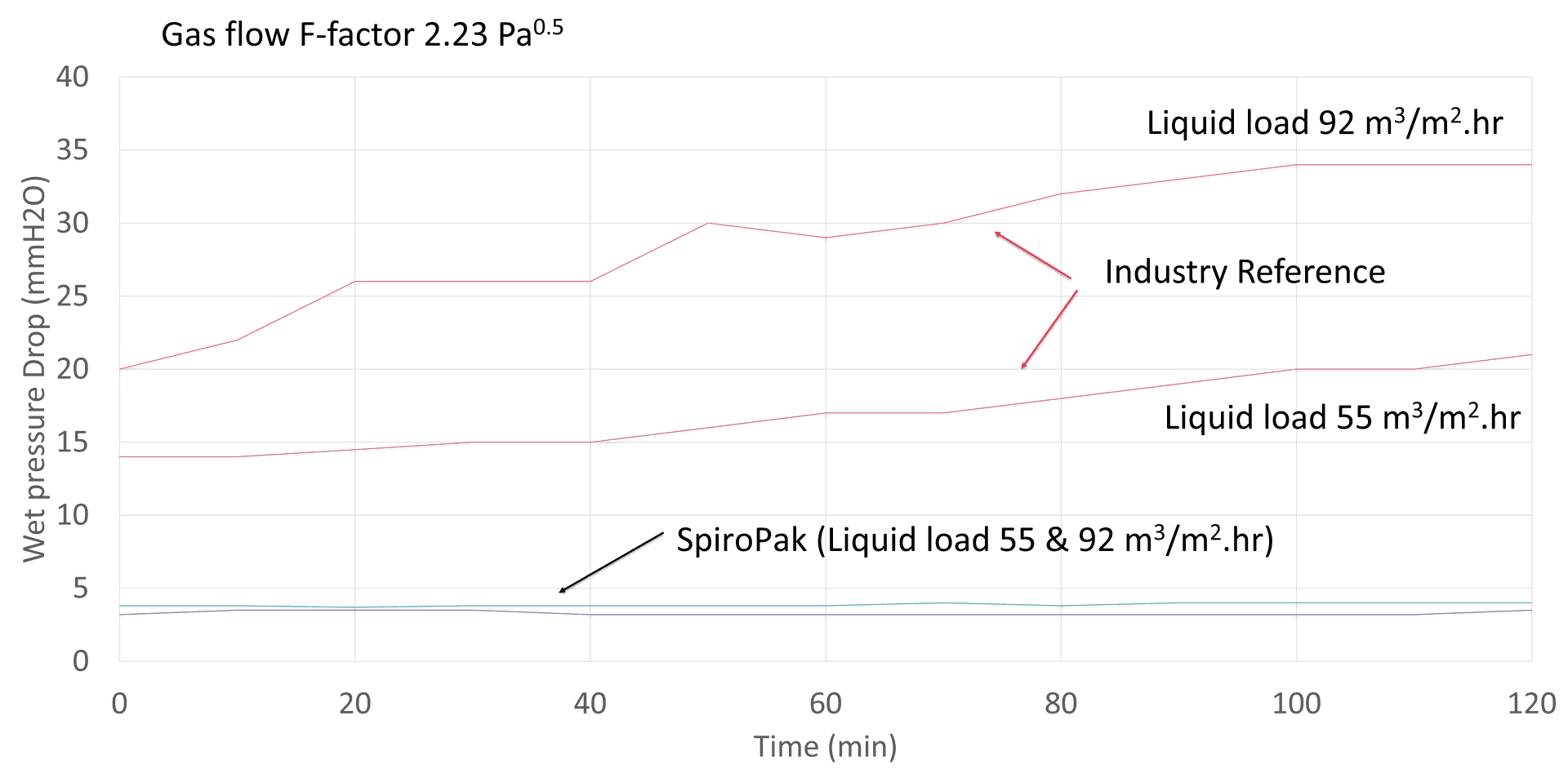
Saturated Salt Solution
The liquid tested is a saturated solution of NaCl in water, known for its strong tendency to form precipitates that can deposit on surfaces.
The SpiroPak data reveals a negligible increase over time, suggesting that fouling is not a major concern in this test. In contrast, the industry reference indicates a continuous rise in pressure drop, which points to significant fouling taking place.
Liquid hold-up
The volume of liquid retained within the structured packing during operation is influenced by factors such as the packing geometry, liquid flow rate, and surface tension. In structured packing, liquid holdup plays a critical role in mass transfer efficiency and pressure drop. While a certain level of liquid holdup is necessary to maintain effective liquid-film coverage for mass transfer, excessive holdup can lead to increased pressure drop and the risk of flooding.
It has been demonstrated that by varying the SpiroPak internal geometry it's possible to match a wide range of liquid hold-up values presented by industry standard products.
Flooding
Flooding occurs in structured packing when the gas and liquid flow rates exceed the packing's capacity, leading to a breakdown in the counter-current flow pattern. As gas velocity increases, it creates greater resistance to the downward flow of liquid, causing liquid to accumulate and obstruct the flow channels. This results in a sharp rise in pressure drop and a loss of separation efficiency. Flooding limits the operational range of structured packing and is a critical design and operating consideration.
It turns out that it's very difficult to flood SpiroPak.
Patents
SpiroPak is patented and has a number of patents pending.
- US: 11602726
- India: 469090
- Japan: 7499230
References
- Sun, B., Bhatelia, T., Utikar, R. P., Evans, G. M., & Pareek, V. K. (2021). Hydrodynamics of a novel 3D printed structured packing–SpiroPak. Chemical Engineering and Processing-Process Intensification, 167, 108533
- Sun, B., Tan, W. S., Bhatelia, T., & Pareek, V. K. (2024). Study on the hydrodynamics of structured packing: Liquid holdup and pressure drop of a novel 3D printed packing. Chemical Engineering Research and Design, 206, 200-209